Cold Weather: How to Maintain Power Plant Readiness and Reliable Operation
Extreme temperature and weather events have become more prevalent in the past decade. The December 2022 Christmas freeze in the southeast U.S. saw many areas experiencing single-digit temperatures. The February 2021 Texas freeze saw temperatures in Dallas reach as low as –2F. Meanwhile, the January–February 2019 Midwest Arctic Polar Vortex saw temperatures plunge as low as –30F.
Each of these events significantly strained electric infrastructure causing inoperable utility equipment and power outages. Within the U.S., many of the regulatory agencies are mandating that resource entities identify cold-weather-critical equipment, develop freeze protection measures for this equipment, and document the minimum ambient dry-bulb temperatures that the resource can reliably operate to. For these mandates, typically, the minimum operating temperature can be based on historical operating data, equipment rating, or engineering assessment. Even more recently, some regulatory agencies have put into place requirements addressing wind speed and wind chill.
Cold weather procedures and equipment changes most common in the colder climates are making their way across the U.S. Generators need to be prepared for cold weather to avoid lost generating ability, which can translate into lost revenue, fines, and equipment damage.
Water and Wind
Water is a major freeze risk, and any equipment that uses water needs to be protected. Systems and equipment not needed during cold weather operation should be removed from service and the water drained to ensure the equipment is not damaged during a freeze event. Water wash systems, inlet chillers, or wet compression systems are examples of equipment that can be removed from service and drained if weather forecasts indicate cold weather approaching; this will allow winterization efforts to focus on items needed for plant operation during a cold weather event.
Some equipment using water will need to remain available, such as NOx water systems, boilers, sensing lines, and heat exchangers. A common way to protect equipment is insulated heat tracing or the addition of a freeze inhibitor (glycol) if the water is part of a closed-loop heat exchange system. Some systems can be drained and then refilled prior to the unit coming online.
Wind on its own cannot cause freezing. The ambient temperature must be below freezing for water to freeze. At temperatures below freezing, wind can rapidly increase the freeze rate by increasing convection, or the rate at which heat is removed from a pipe or other water source. Wind effects can be negated by proper wind breaks and/or insulation.
Equipment Considerations
Fuel Systems. Natural gas is recommended to be maintained above 40F for proper fuel nozzle operation to minimize the condensation of hydrocarbons and moisture in gas. Liquid fuels will have their own minimum temperature that needs to be maintained. Gas lines are always buried below the freeze line, which helps maintain gas temperatures above freezing. It is good practice to insulate the main supply valve, and moisture filter drain lines should be protected to avoid freezing. Heaters may be needed for liquid fuels with minimum temperature requirements.
Gas Turbine Inlet and Bellmouth. Inlet icing or snow accumulation can cause excessive pressure drops, causing unit derate or trip. To avoid this, well-sized hoods should be used to protect the inlet from excessive accumulation. Coalescing-type filters, designed to remove and collect moisture, should be removed before winter.
Compressor bellmouth icing can occur when inlet air is cold and humid, even if the ambient temperature is above freezing. Isentropic acceleration of air can reduce the air temperature by as much as 4F. A viewport can be added to observe the bellmouth (Figure 1). If icing occurs, or a history of icing is known, inlet air heating can be added to avoid foreign object damage from ice ingestion.
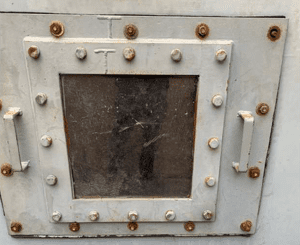
Turbines and Generator. It is recommended to have a heater in each turbine and generator enclosure, dedicated to ensuring critical equipment inside the enclosure is protected. If the turbine and generator are located within a building, the building should incorporate multiple heaters to maintain temperature inside the building. Enclosure or building, doors and vents should be closed to minimize cold air intrusion. During extreme cold events, air entering from an open door or vent can overwhelm the ability of a heater to maintain enclosure temperature.
It is good practice to place turbines on a turning gear at sub-freezing temperatures. This will also keep lube oil flowing. Additional protection may be required for bleed and purge valves, equipment configuration depending.
Generators typically have internal heaters to ensure moisture levels are kept low. These internal heaters for moisture control do not negate the need for a separate compartment or building heater, especially during extreme cold weather events. It is noted that steam turbines are not sensitive to changes in ambient temperatures.
Valves, Instrumentation, Plant Air, and Pumps. Failure of small valves or drains can cause big problems. All critical valves should be insulated, and pressure, flow, and temperature transmitters should be kept in protective boxes with a heat source (Figure 2). Sensing lines utilizing water should be heat traced and insulated.
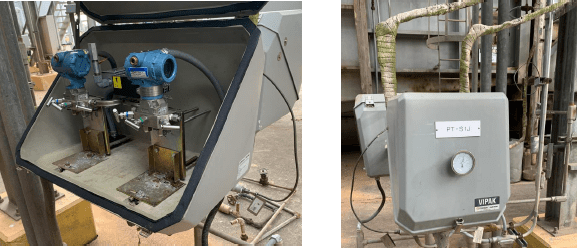
Plant air compressor drains should be kept from freezing and the air dryer should be capable of dropping the dew point by a minimum of 18F. Most dryers are capable well beyond this. Valves that pass undried air, such as compressor bleed valves, are at risk from freezing and should be protected with heat and insulation. Depending on valve position, windbreaks may be necessary.
Water pumps that are critical to plant function must be protected. Submersible pumps that sit in deep wells are typically protected as the water surrounding them does not freeze. In-line pumps, such as boiler feedwater pumps, will have to be protected by a heat source or warm water recirculation and wind breaks.
Lube Oil Systems. It is recommended to have extra immersion heaters available in case of a failure during a cold weather event. It is good practice to check the temperature of lube oil tanks during site rounds, especially at sites configured with exposed lube oil skids. Insulation of exposed lube oil lines may be necessary if sites are prone to experiencing high winds. Lube oil systems on exposed skids may require wind breaks or potentially an enclosure with a heater.
Weather Planning
Winterization Methods. All necessary water systems need to be protected with heat trace and insulation (Figure 3), recirculation from a warm water source, and any water treatment buildings should be heated. Cooling systems, wherever possible, should utilize a glycol-water mixture and all unnecessary water systems should be shut off and drained.

Critical equipment should be protected from the effects of cold wind. Typical protection methods are heat trace and insulation, windbreaks, and/or temporary enclosures with heaters.
Windbreaks should account for prevailing wind direction. Note that windbreaks need to be robust. Tarps tied around equipment will not be as robust as scaffolding wrapped in plastic or metal frames with metal walls (Figure 4). Adequate wind protection will minimize the effect of convective heat transfer.
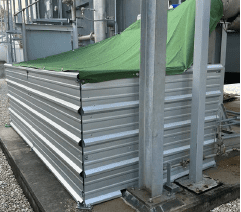
Backup equipment, such as generators or air compressors, may be appropriate if the facility has a history of specific equipment failure during cold weather events. Extra winterization equipment should be kept onsite. This should include tarps, heaters (Figure 5), extension cords, and items to address emergent issues.
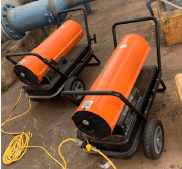
Cold Weather Operating Procedure. Sites should maintain cold weather plans appropriate for the plant location. The intent of a written procedure is to ensure a plan is in place and provides direction for how to keep units operating during cold weather events. Updates to the procedure are a critical part of risk mitigation because equipment failure modes can vary with age; weather patterns can shift; and plant operational modes, configurations, and personal can change. What worked in the past will not necessarily be sufficient in the future. A good cold weather plan should include the following:
- List of cold-weather-critical equipment.
- List of weatherization supplies and equipment.
- Responsible parties and contact information.
- Staffing requirements.
- Plan implementation details, including criteria (calendar date vs. temperature specific).
- Checklists.
- Preparation.
- In-action.
- Post-action/corrective-action.
- Revision control.
- Documentation of historical minimum and maximum temperatures.
- Training requirements.
Summary
Cold weather events will continue to happen. Preparation and planning are critical for plants to remain operational during events.
To meet our customers’ requests to maximize plant availability during cold weather operation, TG Advisors has developed a “Weather Readiness Assessment” that accomplishes three goals through data analysis, review of plant maintenance records, engineering calculations, and expert experience. The assessment:
- Addresses regulatory requests (typically minimum ambient temperature capability and/or wind chill capability).
- Identifies equipment limitations and opportunities for improved robustness.
- Reviews a plant’s weather preparation and action plan and provides feedback for improvement.
TG Advisors’ process includes a plant walkdown and interview with key personnel to review equipment condition and plant configuration and to identify site-specific needs. Please reach out to us with any questions or talk to us about how we can help your site maximize availability during the cold weather season.
—David Butz (dbutz@entrustsol.com) is a senior consulting engineer, and Jason Neville is the engineering manager and a consultant, both with TG Advisors, an ENTRUST Solutions Group company. To learn how to prepare for hot weather, read “Hot Weather: How to Maintain Power Plant Readiness and Reliable Operation.”