Design challenges of repowering steam turbine generator
Image Gallery
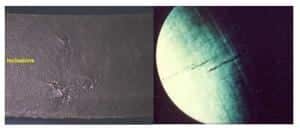
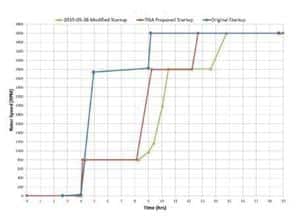
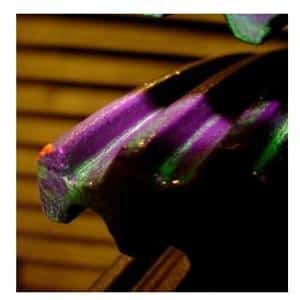
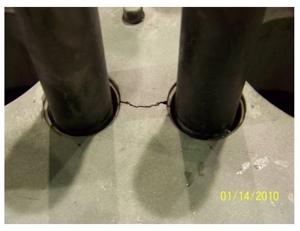
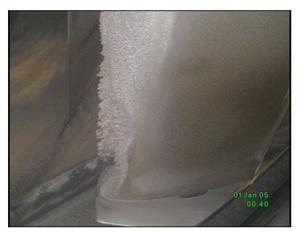
Background
Environmental pressures on conventional fossil fueled boilers has led to a large number of repowering projects utilizing gas turbine technology coupled with a heat recovery steam generator (HRSG) to provide steam to an existing turbine. The economics of utilizing the existing steam turbine generator can be a major factor in the rate of return analysis for these projects. Many repowering projects have been implemented and a number are planned for the near future. In order to improve the success of utilizing an existing steam turbine generator (STG), a number of basic assessments should be considered to ensure safety, long-term reliability and reasonable STG outage repair costs. Highlighted in this article are many of the major factors to consider.
New duty cycle
Many of the STG units that have been repowered were originally designed for baseload operation. Due to the operational flexibility integrated with gas turbine technology, many repowering projects are calling on the steam turbine generator to follow or mimic the gas turbine’s quick on/off and load changing flexibility. The apparent heat rate from the “free steam” available from the HRSG can make the unit much more attractive in merchant plant applications. In addition, most repowering projects for environmental reasons do not have gas turbine bypass stacks, allowing them to operate in simple-cycle operation. Therefore, the steam generated from the HRSG needs to be either bypassed to the condenser or sent to the STG for each and every gas turbine cycle. The STG must undergo a thorough mechanical condition and life assessment to determine if it is capable of operating in this manner without increasing the probability of a major catastrophic failure.
Steam turbine generator factors
Turbine rotor materials
Steam turbine rotor material becomes embrittled when exposed to high steam temperatures and significant service time. When a rotor is embrittled it becomes more susceptible to a rotor burst. In other words, the critical crack sizes required to fail a rotor become very small in an embrittled rotor – cracks might approach the size of those preexisting in the rotor. Therefore, many High and Intermediate Pressure rotors applied in repowering projects might require longer temperature soak periods to enable the rotor to regain ductility before it is ramped up to full speed, where the risks of failure greatly increase (see Figure 1). The need for a longer startup soak period is often overlooked in the economic evaluation of the project.
Existing rotor flaws
There is no rotor operating that does not have a preexisting flaw. It is a matter of how big and if the flaw is located in a high stress region of the rotor (see Figure 2). These flaws typically are evaluated using a fracture mechanics analysis that considers crack growth as a function of the projected duty cycle. In a repowering project that cycles, risks of bore cracking growing to a concerning size increases significantly. Before a project is justified, you should question if boresonic inspections have been considered previously. Are there any life limiting flaws? These concerns should be addressed prior to reuse of rotors in the train, including all turbine and generator rotors.
Rotor attachment concerns
Larger LP blades apply very high centrifugal stresses on the blade attachment area during operation. As the unit cycles on and off, these forces produce a low cycle fatigue concern, which can greatly increase the chances of later stage LP blade cracking. Also, on many older low pressure rotor designs the rotor attachment areas have not been optimized with the latest finite element analysis tools since these were most likely not available when the unit was designed. Stresses are often more concentrated than original design predictions, which increases the probability of low cycle fatigue cracking. This area must be thoroughly evaluated for remaining LCF life based on the projected duty cycle. It should be noted that the material has memory and the damage from prior stop/starts cannot be erased. These cycles must be added to the projected cycling damage to determine remaining life.
LP rotor attachment stress corrosion cracking
Stress corrosion cracking concerns are focused on the stage of the turbine where the steam conditions reach the saturation dome (so called Wilson Line). This is typically in the L-2 or L-1 stages of conventional fossil-fired STGs (see Figure 3). Stress corrosion cracking has an incubation period followed by crack initiation and then propagation. Has the Wilson line has shifted? If so, is the stage more susceptible to SCC with higher stresses or less? If the location is consistent with the prior steam cycle, what is the remaining SCC life? SCC will occur – it is just a matter of when and where. In some applications, SCC occurred as early as 100K operating hours. Is the material used in the repowered STGs more or less susceptible to SCC? Has the project accurately identified steam chemistry monitoring requirements? Has a thorough rotor attachment inspection been made to identify preexisting flaws prior to repowering? These are some of the questions that should be asked and resolved prior to requalifying a turbine for adequate SCC life.
Casing cracking assessment
Almost all casing cracks (including valve bodies) are directly related to low-cycle fatigue loading experienced during on/off and load cycling. The design of casings for LCF life have only recently (last 10-15 years) been optimized with powerful 3D design tools. Therefore, almost all repowering projects that utilize existing casings will have LCF life shortfalls. It is rare for a casing with 20-40 years of service not to have some form of cracking. As noted in Figure 4, LCF cracking occurs in locations where there are significant geometric discontinuities that cause very large stress concentrations. Areas to evaluate are diaphragm ledges, dowel support holes and transitions from small to larger radii. Have the casings been evaluated for LCF life for the repowering project? Have major outage weld repairs been considered in the maintenance budget for the project? If the casing has been identified as a replacement item, has the new casing been optimized for the repowering project duty cycle?
Generator considerations
Some generator rotor designs are highly susceptible to duty cycle related cracking. Specifically, the rotor tooth tops on legacy Westinghouse designs will experience LCF cracking once cycles reach a critical level. Modifications are available to address these failure modes and must be considered in the repowering assessment phase. Most of the time a full rewind of the rotor will be required to accommodate the new lower stressed rotor tooth top geometry. In addition, rotor end winding blocking, pole crossovers and end winding cracking are all issues to be considered in the repowering budget. OEMs have made some significant advancements in respect to addressing known cycling limitations. Most of these modifications can be incorporated easily into existing generator rotor designs. In some cases, the rating of a generator may increase, requiring upgrades in insulation, winding or cooling designs.
Stator and rotor rewind life should always be considered. Rewinding, depending on duty cycle, is needed typically after 25-30 years of service. A rewind also provides an opportunity to re-rate the generator, which will always factor in as a positive in the project justification process.
Turbine blading
Turbine blading can be the most challenging assessment for a repowering project. Inevitably, flow and steam conditions will not match the original design conditions. If the unit will be rated at a higher steam flow, the effects on blade loading and vibratory characteristics must be considered. In many cases, some early stages in the turbine are the limiting factors from the standpoint of passing flow. If there are restrictions based on the new steam conditions, removal of these stages might be required.
In other cases, the new cycle might have increased back end moisture conditions. This will have a detrimental effect on the water droplet erosion characteristic of LP back end blading (see Figure 5). Replacement of older LP blading might be a foregone conclusion. In addition, some OEMs offer higher performance retrofit blades which will fit in the existing rotor attachment. These blades can result in a reduction of heat rate of up to and slightly more than 1 percent for the unit.
Conclusions
Completing a realistic mechanical assessment of the proposed steam turbine generator to be used in a repowering project is essential to ensuring safe, reliable and realistic life projections with the proposed duty cycle. TG Advisers has found some repowering projects have not completed the due diligence and STG upgrades needed for these more stressing applications. As a result, major outage costs and scope have far exceeded the budget estimates in the project’s justification process.
Tom Reid is a consulting engineer for TG Advisers Inc. Tom and team provide engineering services to gas turbine, steam turbine, and generator users worldwide. Tom is a graduate of General Electric’s Edison Engineering Development Program and has numerous patent disclosures related to turbine design and advanced gas turbine repair technology. Tom holds a BSME from Virginia Tech and a MSME from Georgia Tech.