The Future of Hydrogen as a Gas Turbine Fuel
Published on: July 18, 2023
Turbomachinery Magazine, July/August 2023, Volume 64, Issue 4
Running traditional natural gas turbines with hydrogen will play an increasingly important role in reducing CO2 emissions in power generation.
While natural gas is the cleanest large-scale combustion fuel in use today, its use as a fuel for power generation results in approximately 15% of all CO2 emissions in the United States—gas turbines are responsible for a large portion of these emissions. Renewable energy sources are continuing to make inroads into the global energy ecosystem, but gas turbines will continue to be prevalent; therefore, addressing their CO2 emissions is an important step toward achieving a carbon-free energy network.
Hydrogen is earmarked as a possible fuel to displace natural gas and provide CO2-free combustion in gas turbines and beyond. The main byproduct of combusting hydrogen is H2O, making it a truly CO2 emission-free fuel. A long-term goal is to burn 100% green hydrogen in gas turbines, replacing natural gas; in the shorter term, hydrogen can be blended with natural gas and burned in gas turbines for a fractional reduction of CO2 emissions.
Comparison to Natural Gas
When using hydrogen in conjunction with natural gas or as a full replacement, it is important to understand how the two fuels differ. A 100% hydrogen blend requires 208% of additional volumetric flow, roughly three times compared to methane. A 75% blend of hydrogen is required to reduce CO2 emissions by 50%. These percentages make the immediate plug-and-play use of hydrogen in gas turbines difficult.
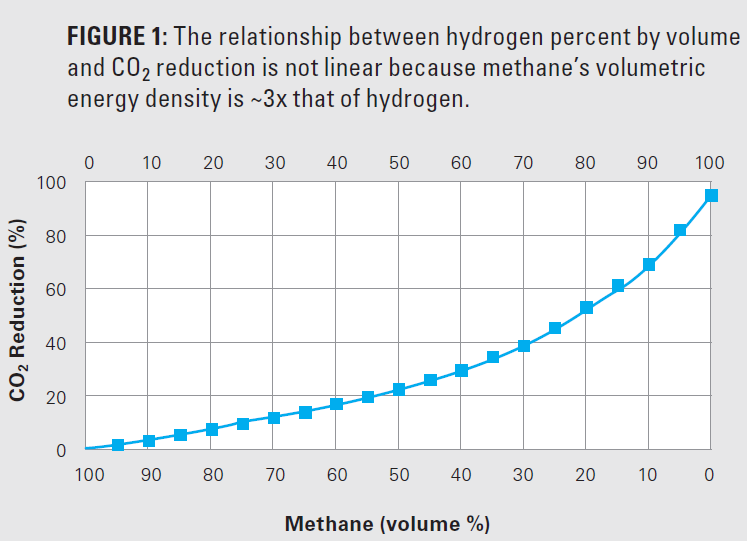
Additionally, hydrogen faces unique supply and infrastructure challenges. Hydrogen’s physical properties make production, storage, and transportation more difficult as compared to natural gas, and it can present safety concerns—such as larger flammability range, lower vapor density, faster flame speed, etc.—that must be considered in system design.
Gas Turbine Considerations
All gas turbines are not created equal. There can be large differences between industrial gas turbines (IGT) and smaller aeroderivative engines as well as across equipment manufacturers. Every gas turbine design needs to be evaluated on an individual basis to determine its hydrogen-burning ability and to what level of retrofit or design change(s) is required to improve
this ability.
Required design changes are highly dependent on the percent volume of hydrogen planned to be burned. Hydrogen burning can be segmented into low-, medium-, and high-percentage blend groups. A turbine operating on a low-percentage blend of hydrogen (5-10%) may not require any design or material changes, as the fuel-burn characteristics are similar to a 100% natural gas fuel stream. For medium-percentage blends (10-50%), the combustor and overall turbine architecture will be mostly unchanged, but design changes to existing combustor materials, fuel nozzles, and control systems will be needed. For higher blends of hydrogen, more than 50%, major modifications must be made to the turbines and likely a complete retrofit of the combustion system. Many OEMs are currently working on new combustion systems that support high-hydrogen blend levels.
Turbine Enclosure
Fuel system piping and valves in the enclosure must be compatible with hydrogen—materials must be hydrogen-compatible and engineering safety factors must be included in the design. Moreover, hydrogen-tight seals must support small hydrogen gas molecules. Piping and valves may have to be enlarged to handle the higher volumetric flow that hydrogen requires, depending on the blending percentage (FIGURE 2).
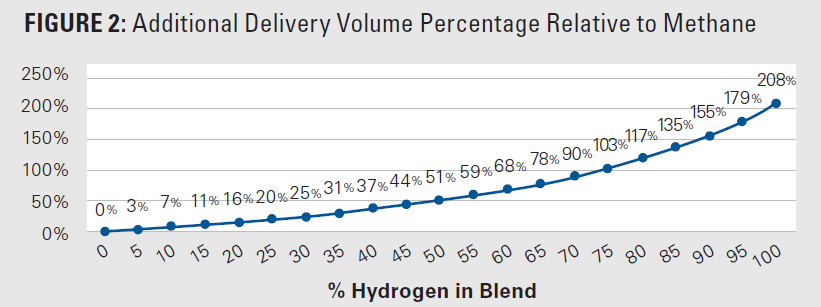
Safety systems for gas detection and fire protection must be modified to account for hydrogen’s volatility and detection differences. Similarly, explosion-proofing must be able to contain larger explosions, and ventilation systems need to be modified.
Combustion System
A turbine’s ability to burn hydrogen is almost solely dependent on the combustion system. The larger the hydrogen percentage in the fuel, the more challenged an unmodified combustion system becomes. To add to the difficulties, for the foreseeable future, combustion systems will have to maintain fuel flexibility and the ability to burn natural gas. The combustion system is challenged by:
- Hydrogen is one-ninth the density of natural gas and is the smallest known molecule, which creates transportation and sealing challenges.
- Hydrogen’s heating value is one-third of natural gas, which means three times as much hydrogen fuel flow is needed to produce the same amount of power as compared to natural gas.
- The flammability range of hydrogen is much larger than that of natural gas, creating elevated environmental, health, and safety concerns for both transporting and burning hydrogen (FIGURE 3).
Advertisement
- Hydrogen burns hotter and has a faster flame speed than natural gas. This creates combustion instability and increases the potential for flame out and flashback.
- Hydrogen flames are much less visible than natural gas flames, making flame detection difficult.
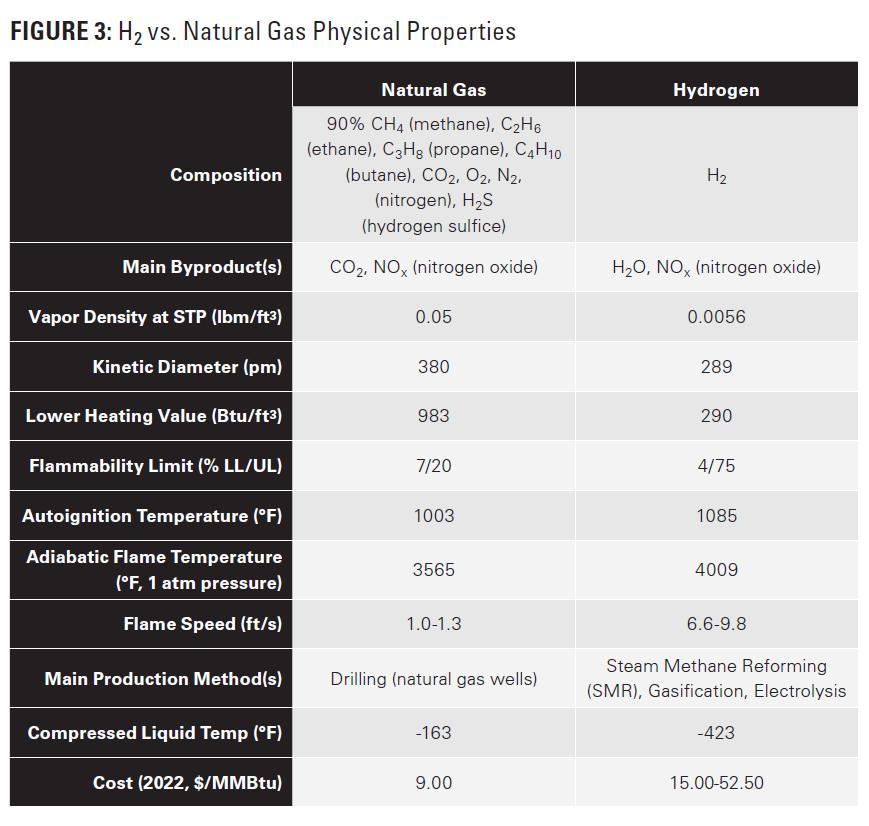
Additionally, hydrogen embrittlement occurs as soon as it is introduced into a system, and it cannot be reversed. Embrittlement lowers the material’s yield stress, which reduces the material’s fatigue capability, particularly for low-cycle fatigue. Temperature, pressure, and stress level can influence the rate or magnitude of embrittlement. However, not all materials are equally prone to hydrogen embrittlement. Both stainless steels and nickel alloys, commonly used in gas turbine combustion systems, experience increased levels of embrittlement at elevated temperatures. This makes combustion material selections for hardware, weld joints, and braze joints difficult.
There are several main combustion system types used throughout IGTs, and the challenges described above will impact these systems differently. The two main combustion system types used in today’s IGTs are diffusion combustion systems and lean premixed combustion systems.
In diffusion flame (or conventional) combustion systems, fuel is directly injected into the reaction zone with no intentional premixing with the combustion air. A diffusion, or non-premixed, flame burns at the flame surface, while fuel on the interior of the flame remains unburned. Diffusion flames generate higher gas temperatures as compared to premixed because the fuel burns close to the stoichiometric ratio.1 The stoichiometric ratio is the ratio between gas and air where complete combustion occurs. High gas temperatures result in lower carbon oxide levels, but higher NOx levels (FIGURE 4).
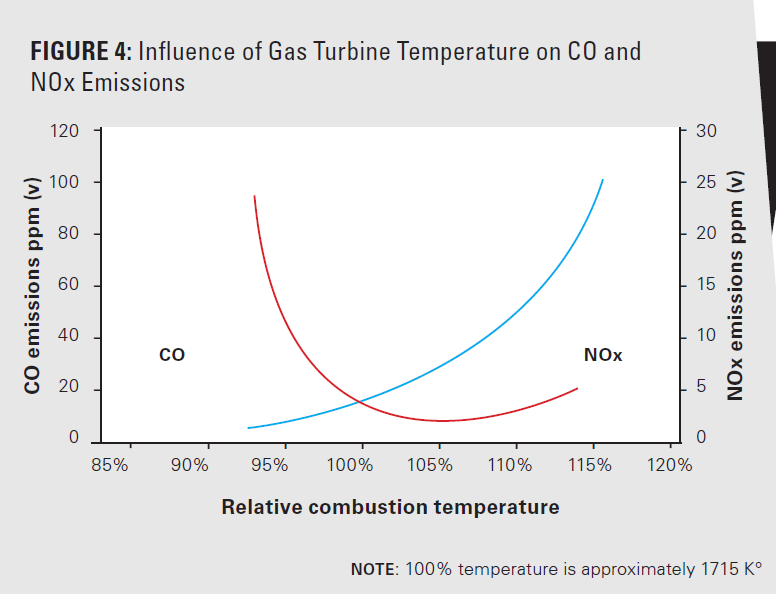
In the primary zone of a diffusion combustor, fuel is injected and burned. Incomplete fuel combustion occurs due to the mixture of fuel and air. A secondary zone, where additional air is added to the combustor, is required to complete full combustion of the fuel. The gas temperatures aft of the primary and secondary zones are too high for downstream turbine component health, thus a dilution zone is used to inject additional air and drop the gas temperature to an acceptable level.
Diffusion combustors offer greater flame stability over a wider range of flame temperatures and fuel compositions, including hydrogen, as compared to lean premixed systems. Because the flame burns close to the stoichiometric ratio, it is less prone to lean blowout during operation; and due to higher gas velocities, it is less likely to flashback. With more flame stability, combustion dynamics remain within acceptable limits. Currently, some diffusion combustors can burn 100% hydrogen, but elevated NOx emissions are expected and require more dilution at the fuel-injection zone.
Due to NOx challenges in diffusion combustors, many of today’s new gas turbine designs are equipped with lean premixed combustion systems: dry low emissions (DLE) and dry low NOx (DLN) combustors. “Dry” indicates that no diluents, such as steam or water, are used for emissions control. While diffusion combustors are currently more capable of burning hydrogen, the gas turbine industry recognizes that lean premixed combustors, with superior emissions control, will continue to be the dominant combustion system for new designs, even with hydrogen.
The main difference between the lean premixed and diffusion combustors is that the fuel and air are mixed prior to injection into the combustion chamber in a lean premixed system. The homogeneous mixture of air and fuel allows for a uniform and lower temperature flame, reducing NOx emissions without the use of dilution and the associated efficiency penalty. Most modern lean premixed combustors also use fuel staging with lean fuel-air ratios to help further control emissions. Lean premixed systems can look vastly different between OEMs and even turbine designs. DLE technology has been continuously evolving, as there has been a constant push for higher efficiencies and lower emissions. The wide variety of designs translates to a large range of hydrogen-burning capabilities across turbines. But today, in almost all cases, lean premixed combustors can handle lower volume percentages of hydrogen when compared to diffusion combustors.
When considering hydrogen in DLE and DLN systems, similar challenges that exist for diffusion combustors are magnified. First, hydrogen’s higher flame speed as compared to natural gas (greater than three times), and the slower moving flame center in a DLE system increases the flashback risk.
Next, the higher flammability range of hydrogen increases the risk of fuel ignition inside the mixing passages. Combustion dynamics are also altered with hydrogen usage. With hydrogen, elevated dynamic amplitudes over a larger range are expected since flame stability is reduced. During transient operations—such as startup and shutdown—dynamics are the greatest concern. And for the foreseeable future, a safe fuel, such as natural gas, will be required for non-steady operation (startup, shutdown, part-load). In summary, the stable operability window for most lean premixed combustors is narrower as compared to diffusion combustors, which means premixed combustors are only capable of lower percent blends of hydrogen.
Compressor
Since all the combustion takes place downstream of the compressor, the combustion of hydrogen does not have a direct impact on the compressor. There are a few indirect impacts that pertain to NOx abatement. There are two possible ways to minimize NOx emissions, either through unit derate or dilution (standard combustor). If unit derate is chosen, the off-design point selected must be acceptable for compressor performance and health. If additional dilution in standard combustors is chosen, the surge margin may be adversely impacted by the change in mass flow of the turbine section relative to the compressor section.
Hot Gas Path
The biggest concern to hot gas path components is the fact that hydrogen’s higher burning temperature increases turbine firing temperature. Additionally, the gas temperature profile leaving the combustor will be hotter and look different when firing hydrogen versus natural gas. For example, the gas temperature profile exiting a diffusion combustor will likely look peakier (highest temperature in the center of the combustor) when burning hydrogen if no additional changes are made. An increase in firing temperature and changes in the combustion profile shape will drive modifications to the component cooling and coating designs to avoid part-life reduction.
Summary
Hydrogen presents an opportunity to drastically reduce CO2 emissions. Many technologies exist or are under development that will help make hydrogen prevalent in the future energy economy. Many of these technologies are very promising, but the major challenges are scale and making hydrogen generation, distribution, and usage economically viable and truly green. Further, gas turbines will continue to be an important part of the world’s energy network as they complement renewable energy sources and have a large existing installed base. OEMs are committing significant resources to design hydrogen-burning technologies into their new engines and to create modification packages for existing engines.
Jason Neville is the Engineering Manager and Consultant at Turbine Generator Advisers, an ENTRUST Solutions Group company.
REFERENCE
1. Greenwood, Stuart A. “Low Emissions Combustion Technology for Stationary Gas Turbine Engines” 2002; Technical Report. San Diego: Solar Turbine Inc., Document.